Tom Gilmartin, PE is Encorus Group’s Director of Engineering and Design Services. He has nearly 30 years of experience as an electrical engineer and project manager, and his work has taken him all over the world. Recently, we asked him about his favorite project.
Of all the projects you’ve worked on throughout your career, which was your favorite?
I designed machines used to make parts for M1-A1 tanks, and commissioned them in Michigan and in Egypt.
Why does this project stand out in your career?
I spent three months in Egypt for it, which was a formative experience in my life at age 24. The culture is so different from ours here in the United States, and it gave me a different perspective on life.
What was unique about this project?
I had to travel all over for this job. I flew from Egypt to England to work with a software supplier, and then had to chaperone three software engineers from England who came to Egypt for the startup.
What was challenging about this project?
So many things were challenging…dealing with the Egyptian military, and the culture divide. There were some incredibly challenging technical problems that had to be solved as well. We had capacitive sensors to detect location, and they kept failing, causing our machine to crash and break parts. There was no internet or even email at this time, so communication was by phone back to the US. At the midpoint of the project, the client was refusing payment, even though they were already using the machine to make parts. I ended up removing the operating system chip from the machine and taking it back to the US. They weren’t happy about it, but we got paid!
What would you do differently if you had the chance to do it over again?
This is a hard question….I was young and clueless about so many things. I’m not sure what I could have done differently, but I probably would be a bit more diplomatic about the issues.
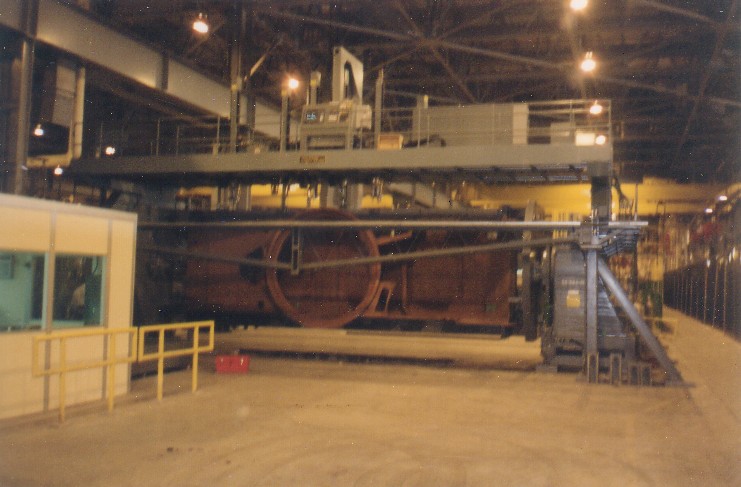
An M1-A1 steel shell is pictured on the machine (gray) with the top of the tank facing in the direction of the photo. The large ring is where the turret mounts for main gun. The machine rotates the 30-ton tank and cuts holes in the top, bottom, and sides. Many holes are cut from steel plates before the shell is welded, but to achieve accuracy, a handful are cut by this machine after welding up the shell. Some parts are 3” thick steel – not easy to cut through!